Why This Matters to Williams
Our employees are the foundation of our company and the reason we continue to transport clean, affordable and reliable energy to millions of people across the country. Williams has a duty to our employees and contractors to establish the governance, practices and training necessary to protect personal safety. Proper workforce safety management is integral to business continuity, regulatory compliance and our reputation—but, above all, it aligns with our ethical standards of conduct.
With oversight from the environmental, health and safety committee of the board of directors, as well as endorsement by our executive management, our Environmental, Health and Safety Policy describes our commitment to integrate workforce safety into our operations, promote awareness among our stakeholders and evaluate our performance for continuous improvement. This policy and our Safety Commitment and Pillars are the foundation of our safety culture and expectations for employees to keep themselves and others safe.
We implement our Environmental, Health and Safety Policy using the Williams Integrated Management System and manage safety risks company-wide through appropriate operating requirements, project standards and site-specific procedures. Our procedures align with Occupational Safety and Health Administration (OSHA) and PHMSA standards.
Any employee or contractor who suspects a hazard, regardless of position or level of responsibility, has Stop Work Authority. At Williams, we champion proactive hazard identification and view Stop Work Authority as an obligation personnel must exercise to protect themselves, the people working beside them and the public. Williams prohibits reprisal against employees and contractors who exercise Stop Work Authority.
We evaluate the effectiveness of our workforce safety management and the strength of our culture using multiple industry-standard metrics. As a result, employee recordable injuries have declined by 31% since 2018. Our safety performance goal for 2023 is to achieve a 10% reduction in the employee recordable incident rate compared to 2022.
Our ultimate objective will always be to eliminate incidents entirely. To achieve this goal, we must continue shifting our safety culture from reactive to proactive. In 2022, we began using the leading indicator of Behavioral Near Miss to Incident Ratio to supplement the traditional lagging indicator metrics used industrywide. This metric captures at-risk behaviors, which allows us to detect and mitigate hazardous scenarios before they manifest into incidents. We set a target of 9:1, or nine at-risk behaviors identified for every one incident with an associated at-risk behavior, and we ended 2022 well above our target at 16.2 behavioral near misses per behavioral incident.
Williams expects every employee and contractor to report all hazards, incidents and near-misses related to personnel and process safety. In 2022, we refreshed our incident severity determination and investigation operating requirements to emphasize the importance of rigorously evaluating and communicating hazards, even those that do not escalate into safety events. Additionally, revisions now clearly delineate incident investigation requirements, which vary based on incident severity.
Williams compiles and regularly shares lessons learned from across the company to accelerate continuous improvement. We distribute all preliminary incident communications for high-potential-severity and high-actual-severity incidents to all employees within one week of the incident. Our health and safety focus team meets monthly to review and approve operating requirements or standard changes that could affect workforce safety. This cross-functional committee includes managers, directors and three individual contributors.
Our Safety Commitment
At Williams, safety is our highest priority. We are committed to Zero Incidents because we care about each other, our families and the communities where we live, work and serve our customers. We are committed to a safety culture that delivers top-tier safety performance through individual ownership, operational discipline, shared learning and prompt action.
WILLIAMS WILL BE THERE
Promoting Hazard Recognition
Our Safe Work Management operating requirement and accompanying mobile application help field employees practice operational discipline and hazard recognition when completing work permitting, work plans and job safety analyses. The industry-leading Safe Work application prompts a series of detailed questions that account for the steps needed to complete safe fieldwork planning, integrates safety plans related to the questions and electronically documents the process to streamline recordkeeping. In 2022, Williams completed more than 267,000 work permits through the Safe Work application, and we project that we will complete our one millionth total permit on the app in 2023. We integrate new capabilities and improvements as we receive employee feedback. In 2022, we integrated 52 changes into the program to reflect updates to our operating requirements, which include task-specific questions and training enhancements for electric work and gas detection processes.
Process Safety
Process safety refers to the systems of management Williams undertakes to prevent uncontrolled, hazardous releases that threaten workforce safety, public safety, our assets, product delivery and the environment. We integrate layers of process safety controls and guidance throughout our operations, from setting our business strategy to operating our facilities so that we can continue to deliver safe and reliable energy. Williams manages our comprehensive set of process safety policies and standards through the Williams Integrated Management System (WIMS). Key policies include pre-startup safety reviews and hazard analysis requirements.
Various regulatory requirements and industry standards set the baseline for our process safety goals. Our uniform approach to process safety reviews uses standardized management of change (MOC) and pre-startup review software, which thoroughly evaluates and tracks modifications to our assets. Additionally, we use a third party to conduct required Process Safety Management (PSM) and Risk Management Plan (RMP) audits across our PSM and RMP-regulated facilities. Although regulations do not require the use of a third party, this gives us an outside perspective on our performance so we can continue to keep our people safe and maintain regulatory compliance.
Williams’ process safety structure includes procedures and equipment to prevent the uncontrolled release of hydrocarbons and hazardous substances. In 2022, Tier 1 and Tier 2 process safety incidents increased by 45%, with 45 events compared to 31 in 2021.[1]
Although Williams has reduced process safety incidents by 40% since 2018, we did not meet our goal to reduce annual process safety incidents by 10% in 2022. To address this performance, Williams chartered a Process Safety Task Force, comprised of process safety, environmental, health and safety, technical services and asset reliability representatives, to drive improvements in our process safety culture and lower the frequency and severity of process safety incidents. Initiatives launched include procedural and tracking improvements to the Safety System Activation program and the creation of franchise-level Loss of Primary Containment (LOPC) review committees. The committees are tasked with reviewing historical enterprise LOPC events to identify potential hazards in their area and share lessons learned. For information about Williams’ LOPC performance and additional asset-specific process safety controls, please refer to the Pipeline and Asset Integrity section.
Robust data collection, performance evaluation and continuous improvement are vital to maintain effective process safety and pursue future improvement. Williams’ process safety group meets quarterly with operations and environmental, health and safety representatives to discuss successes and opportunities for improving our controls. These meetings also drive consistency in implementation across our organization and collaboration with internal and external stakeholder experts. Our senior leaders also regularly review the live performance data dashboard, which tracks process safety incidents and allows us to identify specific issues with equipment types and root causes from an enterprisewide level to individual assets. Additionally, we evaluate our management using an assurance process. Our teams often meet with a safety assurance group to identify, review and discuss solutions to remedy common gaps.
Williams employees undertake Process Safety Management Overview training, which reviews the 14 elements of process safety, such as management of change (MOC), pre-startup safety review, operating procedures and mechanical integrity. Additionally, we distribute quick reference guides to help field staff more easily identify and accurately report accidental ignitions, safety system activations and high-potential process safety near-misses. As with all our workforce safety efforts, we emphasize proactive hazard and near-miss identification and reporting to mitigate incidents before they occur.
[1] After further review of 2021 process safety incidents, one incident was miscalculated and misclassified as Tier 3. This incident was elevated to a Tier 2, based on release quantity, causing the total incidents to increase to 31 for 2021.
Contractor Safety
Williams engages with a diverse group of contractors, subcontractors and suppliers to support our pipelines and assets. We have a responsibility to foster a safe work environment for contractors. We also hold contractors accountable for meeting safety, performance and competency requirements, satisfying contractual requirements and following all applicable laws, regulations and industry standards. To facilitate this, we maintain close communication with contractor groups and support them with safety orientations describing our requirements and potential facility hazards.
Our contractor safety management plan helps us pre-screen contractors, confirm compliance with safety guidelines and monitor performance. Our safety-grading process assesses contractors based on key performance indicators such as total recordable incident rate (TRIR), fatalities, citations, drug and alcohol program compliance and safety management system robustness. Contractors who do not meet our requirements must submit a Contractor Improvement Plan (CIP) detailing their path to compliance. Our environmental, health and safety specialists review CIPs, assign corrective actions and evaluate whether contractors demonstrate improvement against their CIP, which is required to continue business with us. In 2022 we improved our CIP process by creating an electronic portal where plans can be created, reviewed and approved by personnel and leaders. The new process also allows Williams personnel access to view plans created for contractors across the enterprise, which allows for more transparency regarding why contractors are selected. Additionally, we use third-party safety audits to confirm that contractors meet regulatory and contractual requirements. We closely monitor any identified action items and suspend relationships with contractors who fail to close all actions by a set due date, which we sustain until corrective actions are implemented.
To support compliance with our strict safety standards, we work collaboratively with contractors to advance safe practices and integrate contractors into our safety culture. We start each project with a site- and project-specific orientation for all contractors, where we review health and safety management plans. In addition, Williams uses a visitor log system to manage on-site registration and check the status of all contractors entering the site. In 2022, we hosted our contractor safety symposium in Houston with the theme of “Leadership Accountability and Quality of Safety in the Field.”
To promote contractor and process safety, we collect and evaluate contractor safety metrics. We expect contractors to report all incidents and share lessons learned by completing incident investigations. In 2022, our contractor lost-time incident rate (LTIR) was 0.18, and the total recordable incident rate (TRIR) was 0.53.
Safety Training Programs
Comprehensive and relevant safety training is critical to enable employees with the skills and mindset to protect themselves and others. Therefore, we require every employee to complete safety training, with a 2022 completion rate of 98%. We develop unique training plans tailored to individual employees based on tasks they are expected to complete in their roles, as selected by their managers. After completing training, employees must complete written knowledge checks or performance evaluations to demonstrate proficiency.
Reinforcing our company-wide focus on proactive safety, our Hazard Recognition Focus program trains personnel to recognize and act upon workplace hazards before an incident occurs. In 2022, we supplemented this program with a journey of training events where employees can hone their hazard identification and awareness skills. We also developed improvements to our Shifting Gears awards program in 2022, which recognizes and celebrates eleven employees each month who display leadership in identifying and mitigating workplace hazards. These changes will be implemented in 2023.
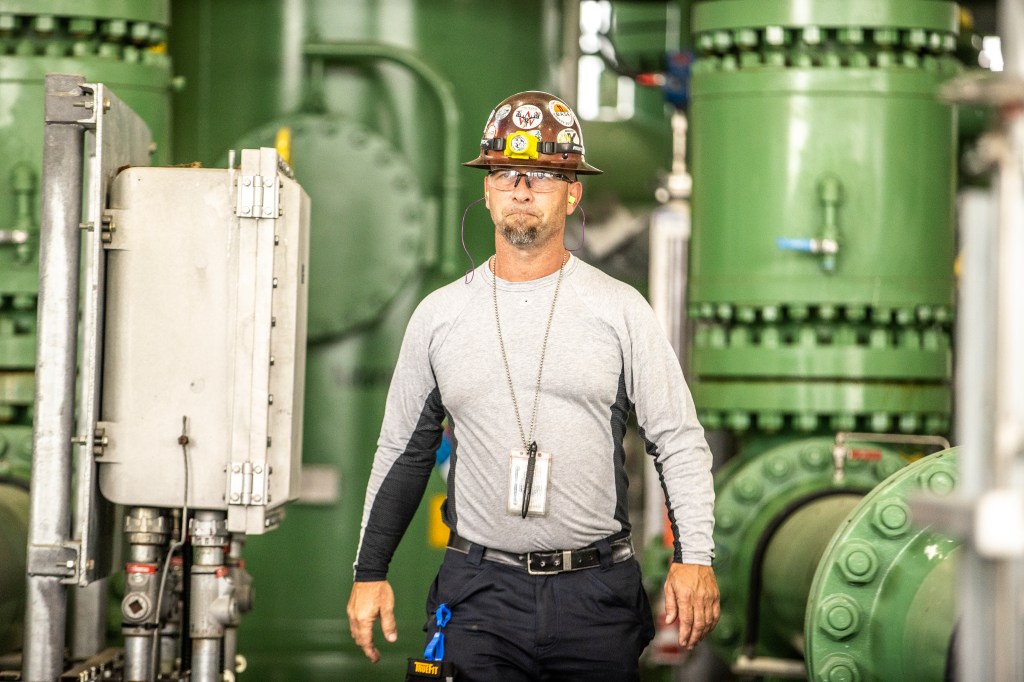
Life Critical Safety
Williams’ safety culture permeates into every decision our field employees make, including how we evaluate hazards, approach new situations, report concerns and view our role within the organization. Therefore, we must understand and regularly reassess the robustness of our safety culture. The Life Critical Field Improvement program is how Williams engages with field employees to survey, train and implement procedures.
A key part of the program is Life Critical Safety Culture Assessments which we perform at each of our 18 regional franchises across our two operating areas. These assessments cover two primary components: 1.) procedure operational discipline reviews, which evaluate how well a franchise is performing in measures like lockout/tagout, and 2.) employee conversations, which are conducted by a third party. Through the employee conversations, the third-party evaluates the franchise safety culture across 25 factors within three drivers: leadership, behavior and competency. Following each baseline assessment, a reassessment is performed within 18 months to track our safety culture evolution and address any regional variation.
Our employee participation across franchises is high, with approximately 80% of employees taking part in conversations with the third-party provider. Since the program launch in 2019, we have completed 18 baseline assessments and eight reassessments. We finalized all baseline assessments in 2022 except for one, which was postponed to effectively account for leadership changes, and we plan to conduct reassessments in 2023 and 2024.
Williams focuses on improving hazard recognition in the field through our Life Critical Safety program. We continue to expand the on-the-job training and feedback portion of this program, allowing leaders to discuss life-critical processes with employees while they perform the task in real-time. This enables employees to raise questions or express concerns immediately. We developed a Life Critical Field Engagement Operating Guideline to integrate this effort across the company, which includes a mobile application, currently in development, where leaders can use prepared questions for on-the-job conversations on various life-critical processes.
Motor Vehicle Safety
Williams field personnel routinely operate motor vehicles when visiting sites and inspecting pipelines. Therefore, we have a responsibility to keep our workforce and the public safe by preventing motor vehicle accidents through robust training, reporting and monitoring. We evaluate and require personnel to report all major and minor incidents.
Our goal is to achieve zero motor vehicle accidents annually. To achieve this, we maintain a driver safety training program and install telematics units in all vehicles to collect metrics on acceleration, cornering, speeding and braking. We share this data with employee leaders and work collaboratively with employees to improve their driving safety behaviors.
We aim to protect employees from potential accidents by performing regular equipment updates and engineering controls. While the total rate of motor vehicle incidents increased in 2022, we achieved a 35% reduction in total vehicle claims costs, indicating that the overall severity of incidents continues to improve. In 2022, our preventable motor vehicle accident rate was 1.89, a 13% increase from 2021.
We have found the greatest opportunity for improvement is reducing low-severity vehicle incidents, such as hitting stationary objects at low speeds. These incidents pose a lesser risk to workforce safety but can cause damage to our assets and vehicles. We continue to advance administrative controls such as training and monitoring. Still, we have shifted our focus to engineering controls such as using smaller vehicles when possible, redesigning parking lots and improving lighting. In 2022, we designed a preventable motor vehicle accident reduction program to evaluate a variety of administrative and engineering controls, including parking lot design, vehicle selection processes, curbing, speed bumps, driving plans and signage, bollard extenders and a 360-degree walkaround program. The Cypress Division of our Eastern Interstates pipeline will pilot this program in 2023.